11. září 2017 00:59
Přehled standardních zkoušek obráběcích strojů 2-2017
Pokračování z minulého čísla
Stroje obklopují moderního člověka v dosud nebývalé míře. Stále ještě platí, že člověku slouží, i když čapkovská vize vzpoury robotů klepe na dveře a začíná plnit stránky mnohých časopisů.
Zkouška opakovatelnosti nastavení polohy je určená jen pro NC stroje. Postupuje se dle normy ČSN ISO 230-2: 1997. Zkouška se provádí pro lineární i rotační osy. Data se měří jednopaprskovým laser-interferometrem a odražečem, pro rotační osy s použitím tzv. „rotačního stolku“. Důležitý je dohodnutý zahřívací cyklus stroje a udržování tepelného pole stroje během zkoušky v dohodnutých tolerancích.
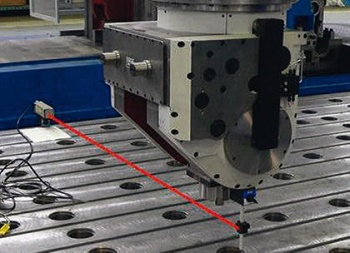
Obr. 1
Určení přesnosti nastavení polohy na diagonálách tělesa a stěn (Zkouška diagonálního přestavení) Zkouška diagonálního přestavení byla zavedena nedávno. Norma ČSN ISO 230-6 je z roku 2003. Je to obdoba zkoušky přesnosti nastavení polohy v ose, avšak odchylky nastavení polohy se měří diagonálně, za současného pohybu více pohybových os, viz obr. 2. Cílem je stanovit tzv. volumetrickou přesnost stroje, čili přesnost polohování v celém pracovním prostoru. Přesnost nastavení polohy v jednotlivých NC osách totiž ukazuje pouze vlastnosti stroje v těsné blízkosti těchto os a neříká nic o přesnosti obrábění ve vzdálených pozicích nástrojů uvnitř pracovního prostoru. Některé řídicí systémy disponují i softwarovými kompenzacemi nastavení polohování jednotlivých os podle dat získaných měřením přesnosti v diagonálách tělesa. Zkouška přesnosti diagonálního přestavení trvá sice poměrně dlouho, ale zato poskytuje informace, které nelze jinak úsporněji získat.
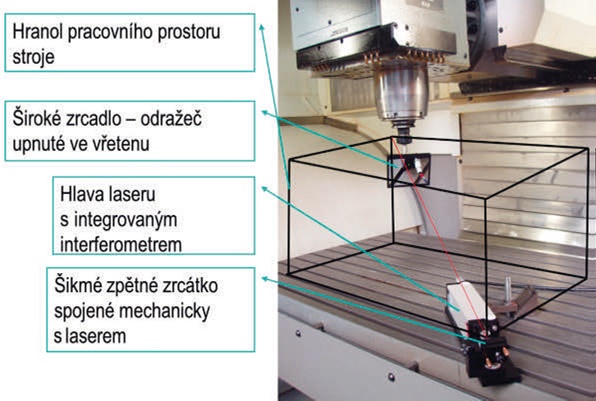
Obr. 2
Zkouška kruhové interpolace u číslicově řízených obráběcích strojů. Mezi zkoušky přesnosti řadíme i tzv. „Kruhovku“. Metodicky se řídí normou ČSN ISO 230-4:2010. Měřicí přístroje jsou popsány v ISO 230-1:1996. Obvykle se k měření používá přístroj anglické firmy Renishaw zvaný Ball-bar. Český název neexistuje. Angličtina výborně vystihuje vnější vzhled přístroje, který skutečně vypadá jako tyčka se dvěma kuličkami, viz obr. 3. Ve skutečnosti obsahuje Ball-bar citlivý snímač vzdálenosti mezi dvěma kuličkami, které se otáčí ve svých přesných lůžkách během kruhového pohybu. Metoda se používá pro měření na frézkách i na soustruzích. Vždy jde o stanovení odchylek při současném pohybu dvou lineárních NC os, které ovládají pohyb nástroje a vytváří (interpolují) jeho kruhovou dráhu. Při měření se simuluje pohyb nástroje ve směru a také proti směru pohybu hodinových ručiček a hodnotí se rozdíly mezi oběma skutečnými drahami. Zkouška kruhové interpolace patří mezi ty jednodušší, časově nenáročné zkoušky, ale je schopna odhalit širokou škálu geometrických odchylek stroje (kolmosti os, nastavení servopohonů, chyby polohování, vůle v osách atp.).
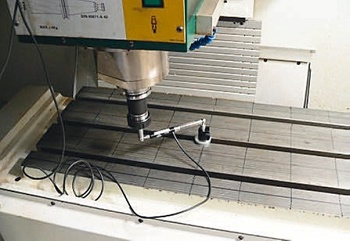
Obr. 3
Další zkouška přesnosti pětiosých strojů se nazývá Stanovení přesnosti transformace lineárních souřadnic X, Y a Z při současném pohybu s některou z rotačních os A nebo C. Můžeme ji zařadit pod normu ISO 10791-6:2014, „Geometrická přesnost rotačních os (přesnost vřeten, otočných a naklápěcích hlav a stolů)“. Způsobů jak změřit případné odchylky od ideálního, vzájemného pohybu os je mnoho. Jednou z možností je použít speciální měřicí hlavy se třemi kontaktními snímači výchylky, které tvoří lůžko pro přesnou kouli, jejíž odchylky od ideální polohy snímače měří. Pokud by součinnost pohybu rotační osy a spolupracujících lineárních os byla ideální, poloha přesné koule v jejím lůžku by se neměnila a snímače by zaznamenaly nulový pohyb. Uspořádání při měření je na obr. 4.
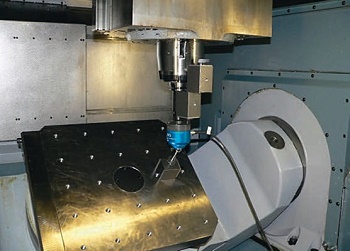
Obr. 4
Zkoušky přesnosti obráběcích strojů tvoří soubor, který poskytuje ucelené informace o přesnosti stroje. Výsledky odráží jak vliv přesnosti výroby dílců stroje a jejich montáže, tak určitý vliv seřízení pohonů na přesnost obrobku a také vliv tepla vznikajícího při činnosti stroje i tepla působícího v okolí stroje. Spolu s doporučenými tolerancemi přesnosti, případně s výsledky zkoušky pracovní přesnosti při obrábění zkušebního obrobku, se údaje o geometrické přesnosti nejčastěji používají k účelům přejímky obráběcích strojů. Slouží i k pozdější kontrole stavu strojů (stupně opotřebení), kde se obvykle doplňují diagnostickým měřením vynucených vibrací.
Vlivy zdrojů tepla
Zkoušky, kterými se stanoví významné zdroje tepla rozmístěné ve stroji i mimo něj, doporučuje norma ČSN ISO 230-3. Teplota značně ovlivňuje přesnost obrábění prostřednictvím dilatací materiálů, ze kterých je stroj zhotoven. Dílce stroje, vyrobené šedé litiny nebo z oceli, se při zvýšení teploty dílce o jeden stupeň Celsia prodlouží o 0,01 mm na každý metr své délky.
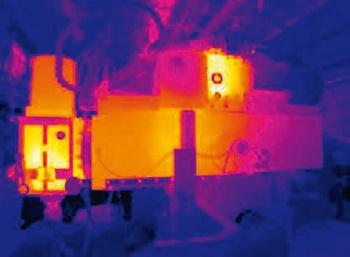
Obr. 5
Někdy značné tepelné záření působí na stroj z vnějšku, z okolí stroje. To jsou např. atmosférické jevy, teplo vyzařované z okolních strojů, z topidel a klimatizací. Teplo vzniká i uvnitř struktury stroje v důsledku mechanických i elektrických vlastností dílčích agregátů ve stroji pracujících, v důsledku tření v pohyblivých spojeních různých dílů stroje nebo elektrických ztrát ve vinutí motorů a v neposlední řadě i v důsledku samotného řezného procesu dělením obráběného materiálu. Různorodost zdrojů tepla a časově proměnlivý tok tepelné energie strojem spolu s tvarovou a rozměrovou variabilitou stroje způsobují nerovnoměrnost rozložení tepelné energie ve struktuře stroje, a tím i proměnlivé dilatace v čase i prostoru. K tomu se přidružuje různorodost konstrukčních materiálů a mnohotvárnost součástí stroje, což se navenek projevuje různou schopností součástí pojmout tepelnou energii a dále ji předat do nejbližšího okolí. Konečným důsledkem těchto složitých vztahů jsou časově proměnlivé odchylky stroje od přesného geometrického tvaru, které se v různé míře transformují ve finální nepřesnosti obrobků. Velmi názorné výsledky poskytuje měření teplotních polí pomocí termokamery. Příklad je na obr. 5. Na snímku jsou zřetelné dva hlavní tepelné zdroje, pohon a vřeteno. Měření tepelných deformací v místě frézovacího nástroje ilustruje obr. 6. Místo nástroje je upnut přesný trn. Odchylky (teplotní drifty) měří čtyři radiální a jeden axiální bezkontaktní snímač výchylky. Data se registrují plynule v digitální i grafické podobě. Po analýze dat naměřených různými způsoby lze optimalizovat rozmístění vnějších i vnitřních tepelných zdrojů a současně zvážit možnosti chladicích okruhů. To vše s cílem minimalizovat tepelné deformace stroje.
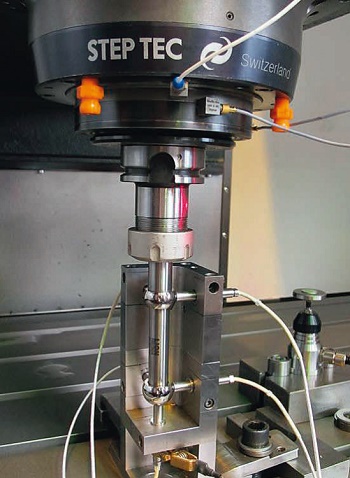
Obr. 6
Měření emise hluku
Měření emisních hodnot hluku u obráběcích strojů slouží hlavně pro deklaraci stavu stroje ve vztahu k hygienickým požadavkům. Je také součástí CE a hodnota emisní hladiny akustického tlaku LpA a hladina akustického výkonu LwA by měla být uvedena v návodu pro obsluhu stroje. LpA vyjadřuje možný příspěvek stroje k celkové hlučnosti na pracovišti, zatímco LwA vyjadřuje celkový akustický výkon stroje, tedy parametr, který slouží pro vzájemné porovnání strojů z hlediska hlučnosti (známe např. z civilního života při nákupu el. spotřebičů).
Akustický tlak nebo akustická intenzita může také sloužit pro lokalizaci zdroje hluku, tedy pro diagnostické účely. Vytvářejí se tak tzv. intenzitní mapy, kde jsou barevně vyznačena místa s největší emisí hluku. Těchto měření využíváme ke snižování hlučnosti strojů.
Stanovení úrovní vibrací, vibrační diagnostika
Jestliže stroj, jak při chodu naprázdno, tak při obrábění, vibruje, je třeba změřit úroveň vibrací podél jeho struktury a z analýzy dat odvodit vhodná opatření ke snížení chvění. Velmi často se jedná o nevyvážené rotující součásti. Zvláštním případem zdrojů vibrací jsou pohyby posuvových os (a to zejména při náhlých změnách rychlosti pohybu, při tvrdém nastavení pohonů a při různých typech křížení vedení a při nadměrných vůlích v uložení). Všechny tyto poruchy je třeba umět identifikovat, ať už s pomocí měření geometrické přesnosti, vibrační diagnostikou anebo analýzou nastavení pohonu.
Kromě toho může některý rotor pracovat v blízkosti některé z vlastních frekvencí nosné struktury stroje. Má-li přitom některá část nosné struktury nízkou dynamickou tuhost, vybudí rotor vibrace s vysokými amplitudami. Tyto vady odhalí např. rozběhový test. Na obr. 7 vidíme jeho výsledek s vrcholy vibrací v oblasti 7 500 až 8 500 1/min.
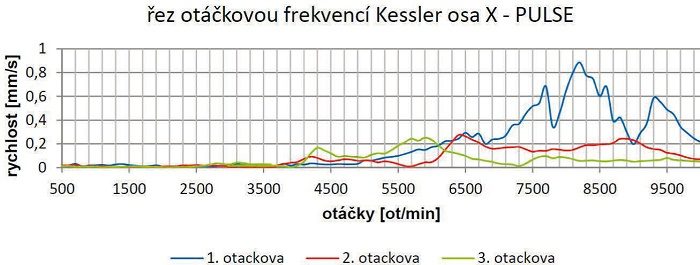
Obr. 7
Tento graf je řezem spektrogramu rozběhu stroje pro specifické frekvence (zde otáčková frekvence a její harmonické násobky). To už se ovšem dostáváme ke složité analýze vibračního signálu. V nejjednodušší podobě je reprezentativním parametrem vibrací tzv. celková efektivní hodnota vibrací, což je jedno číslo, které vyjadřuje velikost vibrací pro stanovený frekvenční rozsah. Tato hodnota je pak porovnávána s povolenými hodnotami v příslušných normách (např. ČSN 20 0065 pro vibrace obráběcích strojů).
Zkouška statické tuhosti stroje
Pracovní přesnost obráběcího stroje přímo souvisí s úrovní statické tuhosti. Nosná struktura obráběcích strojů se navrhuje tak, aby statická tuhost byla co nejvyšší při co nejnižší hmotnosti. Tato optimalizace se prověřuje na prototypu silovým zatížením stroje v místě obrábění (v místě nástroje) a měřením odpovídacích deformací podél hlavních nosných prvků struktury, obr. 8. Deformace se měří vůči silově nezatíženému rámu. Z analýzy naměřených dat plyne rozmístění slabých míst konstrukce.
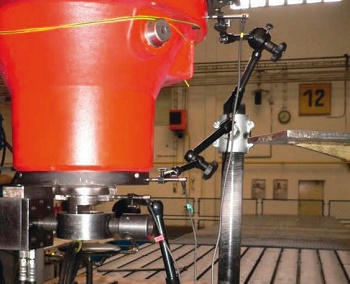
Obr. 8
Zkouška dynamické tuhosti stroje a stability řezného procesu
Nízká dynamická tuhost obráběcího stroje způsobí vysoké vibrace vznikající pouze při procesu obrábění. Jejich důsledkem je především velmi nekvalitně obrobený povrch součásti, ale i možné poškození břitu nástroje a nadměrná hlučnost. Dynamická tuhost se pro tento případ prověřuje měřením frekvenčních charakteristik stroje v místě upnutí nástroje. Z charakteristik lze určit frekvenci nežádoucích vibrací. Následně se speciálním měřením určí, které části stroje se při této frekvenci nejvíce chvějí. Na obr. 9 je příklad výsledku měření lože, svislého stojanu se saněmi, v nichž je upevněno vodorovné smykadlo nesoucí frézovací hlavu. Je vidět, že v tomto případě je na vině vodorovné smykadlo. Nižší úroveň mají vibrace svislého stojanu. Jsou-li vysoké vibrace způsobeny malou tuhostí nosných prvků, je náprava nákladná a je možná jen při vývoji prototypu. Je ale časté, že výsledná nízká tuhost je způsobena netuhými spoji dílců nosné struktury. V tom případě bývá oprava jednodušší.
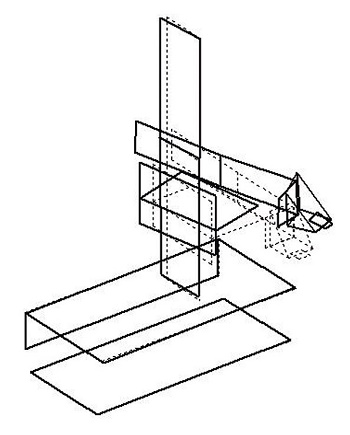
Obr. 9
Existuje ještě jeden zdroj vibrací, a to je proces obrábění. Odborně se vibracím při obrábění říká „nestabilní obrábění“, či „nestabilita“, „nestabilní řez“. K nalezení stabilních podmínek obrábění je třeba speciálního měření a následně výpočtů tzv. diagramu stability, obr. 10. Ten lze vypočítat na základě změřené frekvenční charakteristiky (FRF v obrázku) a slouží k nalezení nejvyššího možného průřezu třísky, při kterém vibrace (při daných otáčkách vřetena nebo dané řezné rychlosti a posuvové rychlosti) nevzniknou.
Ve Výzkumném centru pro strojírenskou výrobní techniku a technologii při Fakultě strojní ČVUT v Praze byla vybudována akreditovaná zkušební laboratoř disponující přístroji schopnými měřit podle uvedené normy ČSN ISO 230. Personál laboratoře je vyškolen patřičným způsobem podle zásad systému kvality normy ČSN EN ISO/IEC 17025.
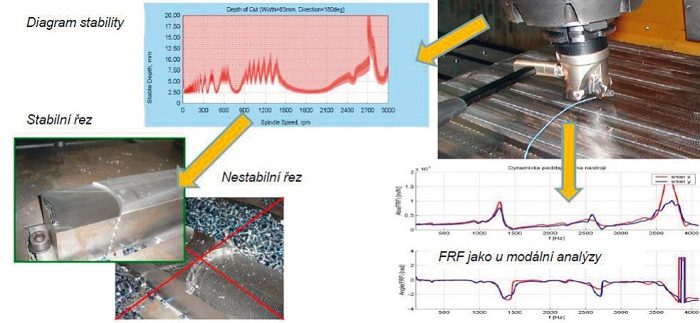
Obr. 10
Způsobilost laboratoře je každoročně kontrolována nezávislým auditem ČIA. Standardizované metody se používají proto, aby se zaručila jednotná metodika měření, a tím i srovnatelné výsledky. Tam, kde nejsou normy k dispozici, měří se dle schválených interních metodických předpisů. To se týká hlavně zkoušek potřebných při výzkumu vlastností strojů, které se uplatňují v případech podstatných konstrukčních změn, kdy je třeba prověřit vliv těchto změn na užitné vlastnosti stroje, nebo při optimalizaci řezných procesů např. s novými řeznými nástroji nebo materiály obrobků. Podrobněji se k jednotlivým zkouškám vrátíme v dalších číslech časopisu.
P. Chvojka, D. Burian, M. Janota, P. Bach, Akreditovaná zkušebna Výzkumného centra pro strojírenskou výrobní techniku a technologii při strojní fakultě ČVUT v Praze
Mohlo by se Vám líbit
Cílem je stát se jedničkou pro oblast kabelů
- Elektro
-
10. července 2025
Společnost KONEKA, která vznikla vloni na podzim jako dceřiná společnost PRAKAB (PRAKAB Pražská Kabelovna s.r.o.), plánuje v letošním roce dále rozšiřovat své služby a produktové portfolio. […]
Každý den je jinak BAREVNÝ!
- Plasty
-
08. července 2025
Chcete si pověsit na zeď něco barevného a užitečného? Připravili jsme pro Vás nový plakát se základními informacemi o barevném prostoru CIELab a výpočty ΔE […]
Nové elektrické polohovací zařízení HIWIN: Spolehlivý a přesný lineární pohyb
- Automotive
-
08. července 2025
Jedinečné na trhu díky přídavnému podpůrnému vedení HIWIN, přední výrobce lineárního vedení, kuličkových šroubů a polohovacích zařízení, představil na letošním veletrhu Automatica 2025 v Mnichově […]