06. června 2018 00:19
Rychleji, a přesto bezpečněji …
Monolitní frézy Seco Jabro pro pokročilé hrubování (AR)
Definuje strategie frézování obráběcí nástroj, nebo je tomu naopak? V současné situaci průmyslové výroby nabývá tato otázka na významu. Obrobky jsou stále složitějších tvarů a převážně z obtížněji obrobitelných materiálů. Výrobní dávky se zmenšují, třeba až na úroveň jednotek kusů, a naopak vzrůstá variabilita typových dílců – požadavek individualizace je heslem moderní doby. Jak nejlépe vyhovět trendům Industry 4.0 – metody, která tuto situaci řeší – z pohledu obráběcích nástrojů?
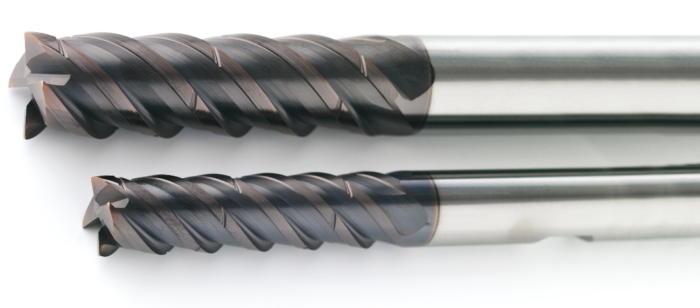
Monolitní frézy řady JS560 AR
Ve smyslu požadavků na obráběcí operace jde o vysokou spolehlivost, výrobní i nákladovou efektivitu a univerzálnost nástrojového vybavení i strategií obrábění. Spolehlivostí se rozumí výstup správného počtu obrobků v požadované kvalitě a ve sjednaném termínu. Průběh obráběcích operací musí mít tedy vysokou bezpečnost, aby nebyl proces výroby nikterak narušován. Nástroje nesmí být přetěžovány, musí být schopné obrábět různé materiály a standardně vykazovat opakovatelnou trvanlivost břitů. Vysoká produktivita a nízká nákladovost musí být zachovány v průběhu různých typů obráběcích operací a velmi výhodná je i možnost využití různých strategií obrábění. Z tohoto pohledu je tedy zřejmé, že nároky na obráběcí nástroje jsou a budou čím dál tím vyšší.
Názorným příkladem nového pohledu na využití dobře známých a osvědčených obráběcích nástrojů je využití monolitních karbidových fréz. Již od prvních typů uvedených na trh představovaly karbidové frézy vysoký kvalitativní skok v produktivitě obrábění oproti nástrojům z rychlořezné oceli. Po dlouhou dobu však tato skutečnost představovala jediný rozdíl, neboť metody frézování zůstávaly stejné a měnily se pouze řezné podmínky. S rozvojem možností obráběcích strojů a jejich řídicích systémů se postupně začaly objevovat nástroje nových typů, a tak se můžeme v praxi setkávat s nástroji pro vysokoposuvové (HFM), vysokorychlostní (HSM) či vysokovýkonné (HPM) frézování. Na zcela novou úroveň využití pak pozdvihl využití monolitních karbidových fréz vývoj CAM systémů. Programování komplexních drah nástrojů a dynamické úpravy řezných parametrů v průběhu procesu umožňují zásadní změny v nasazení těchto nástrojů a využití jejich potenciálu v daleko širším měřítku.
Uvedený přístup také ukazuje jednu stranu možné odpovědi na otázku v úvodu tohoto článku. V tomto případě se skutečně provedení a vlastnosti nástroje podřizují strategii jeho použití, aby byl výsledný efekt co nejvyšší. Jde přitom o výsledek mnoha úprav základní konstrukce nástroje, který stál na počátku této převratné technologie. Začínalo se totiž nasazením univerzálních čelních válcových fréz, které byly běžně k dispozici pro konvenční způsoby obrábění. Takové provedení dobře vyhovuje filosofii využití
celé délky bočních břitů nástroje, které zůstávaly při běžném použití často prakticky nedotčeny, zatímco čelní část mohla být až nevratně poškozena. V sortimentu Seco takové nástroje představuje řada vysoce univerzálních fréz, řada Jabro Solid2 – JS550. Tyto nástroje, ve třízubém (JS553) nebo čtyřzubém (JS554) provedení jsou určeny především k produktivnímu hrubovacímu frézování prakticky všech druhů materiálů. Dodávají se navíc v několika délkových řadách, a tak je možné vybrat nejvhodnější kombinaci rozměrů ze širokého sortimentu provedení. Řada JS550 stále představuje jeden z nejúspěšnějších a nejprodávanějších nástrojových programů v rámci Seco.
Vyústěním snahy o využití některých faktorů procesu frézování, „zajímavých“ pro zvýšení produktivity operací, prodloužení trvanlivosti nástroje a vyšší spolehlivost výroby, jakými jsou například dodržení střední tloušťky třísky, úhlu opásání nástroje či využití malé radiální hloubky záběru, byla metoda trochoidního frézování po přímé ose. Relativně jednoduchý cyklický pohyb středu nástroje bylo možno zadat do běžného řídicího systému většiny strojů jako tabulku X a Y souřadnic a využít tak krátké doby styku břitu nástroje s materiálem obrobku ve smyslu nízkého zatížení a malého množství tepla při velké axiální hloubce řezu. Trochoidní frézování se brzy stalo jedním ze standardních cyklů u CNC strojů a prudký rozvoj výpočetní techniky umožnil vývoj a nástup CAM softwarů, které základní možnosti řízení obrovsky rozšiřují. Náhle nebyl problém celkem snadno programovat nelineární dráhy nástroje a ještě v průběhu obrábění měnit jeho parametry. Dalším stupněm pak byla možnost využití CAD modelů obráběných součástí a počítačový návrh postupu odebírání materiálu z výchozího polotovaru, včetně antikolizní simulace procesu.
Při použití standardních nástrojů pro různé strategie dynamického a adaptivního obrábění se však ukázalo, že jejich schopnosti jsou v tomto oboru omezující. Pro plné využití možností bylo třeba některé vlastnosti fréz upravit, a tak postupem vznikly nástroje plně koncipované pro tyto moderní metody obrábění. V roce 2012 tak Seco uvádí na trh jeden z prvních nástrojů, primárně určených pro metody pokročilého bočního hrubování (AR = Advanced Roughing), frézu JS554-3C. Dalším krokem bylo provedení JS554-2C v roce 2015, avšak ani zde se vývoj nemohl zastavit. V současné době totiž představují AR metody více než 50 % aplikací v leteckém a 30–40 % v ostatních moderních segmentech průmyslu obrábění. Spolehlivost metody je zásadním přínosem v možnosti automatizace procesů na cestě Industry 4.0. Proto se v roce 2016 dostává na trh nástrojová řada Seco Jabro JS560 AR. Nástroje ve čtyřzubém (JS564) a pětizubém provedení (JS565) zahrnují všechny konstrukční prvky, které umožňují jejich maximální výkonnost při AR obrábění, přičemž si nástroje zachovávají schopnost šikmého zafrézování či čelního frézování po vrstvách (Z-levelling), aby neztratily na univerzalitě v metodách obrábění, a jejich řezná geometrie vyhovuje obrábění různých materiálů ze skupin ocelí, austenitických nerezových ocelí či superslitin. Konstrukční i řezná geometrie těchto nástrojů je vysoce komplexní a proměnlivá jak v axiálním, tak i radiálním směru vůči ose nástroje. Dokladem toho, do jakých technických detailů je třeba zasáhnout, je otázka radiálních děličů třísek na ostří nástroje. Přestože se jedná o vysoce funkční prvek, způsobující vznik kratších třísek (a tedy vyšší bezpečnost procesu obrábění v celkovém kontextu), jdeme vlastně proti osvědčené poučce, že ostří má být co nejcelistvější a bez vrubů, které by mohly způsobovat vznik prasklin a snížení spolehlivosti (tj. trvanlivosti a bezpečnosti) nástroje. Proto se na základě zkušeností v průběhu vývoje a používání nástrojů profil a velikost děličů již dvakrát měnily tak, aby bezpečnost na jedné straně nebyla vykoupena rizikem na straně druhé.
Účinnost monolitní karbidové frézy Seco Jabro JS565 výstižně dokládá následující příklad z praxe (obrázky níže). V obrobku z oceli 14 220.3 bylo třeba vyfrézovat 3 kapsy o rozměrech 100 × 53 mm a hloubce 55 mm. Původní metodou hrubování na stroji Makino A81M s kuželem ISO50 bylo frézování vysokým posuvem a obrobení dílce trvalo přibližně 45 minut. Reakcí Seco na požadavek zkrácení času výroby byla příprava zcela odlišné technologie –pokročilého bočního hrubování (AR) pomocí monolitní karbidové frézy JS565160D3C.3Z5C-NXT o průměru 16 mm a s délkou bočních břitů 55 mm. Operace započala vyvrtáním výchozího otvoru na plnou hloubku. Poté nastoupila pětizubá fréza chlazená emulzí a při řezné rychlosti 365 m/min (7 100 ot/min) a posuvu na zub 0,168 mm/zub (rychlost posuvu 5 968 mm/min) v axiálním záběru 38 mm (+ zbytek do 55 mm ve druhém záběru) s radiálním krokem 1 mm obrobila všechny 3 kapsy za 10 minut. Po odzkoušení při hloubce řezu 38 mm, kdy nedocházelo k žádným problémům s třískami, vibracím ani rozměrovým nepřesnostem byla pro další obrábění zvětšena právě axiální hloubka řezu na 55 mm (což je také maximální délka bočních břitů nástroje), a tak se podařilo zkrátit celkový čas obrábění o dalších 50 %, tedy na konečných 5 minut na 3 kapsy. Dalším velkým přínosem se ukázala trvanlivost břitů nástroje, které ani po 300 minutách v řezu nevykazovaly takové opotřebení, že by bylo nutno nástroj vyřadit a nasadit nový.
Jaká je tedy správná odpověď na otázku v záhlaví článku? Pokud zvolíme pro obrábění určitou metodu, měli bychom pro její plné využití sáhnout i po nejvhodnějším nástroji. Přitom však nesmíme ztrácet ze zřetele, že pokud budou například rozměry obráběného typového prvku značně rozdílné, bude třeba na místě použít jinou metodu i nástroj. Na druhou stranu je dobré znát možnosti obrábění nástrojů, které již máme ve svém provozu k dispozici a začít je využívat „nekonvenčním“ způsobem – mnoho z nich nám to totiž umožňuje. Pro výrobu několika kusů pak není třeba pořizovat nové nástroje a připravovat kompletní program. Využívejme to, co máme, tím nejlepším způsobem, a pokud připravujeme novou, rozsáhlejší výrobu, pořiďme si ty nejvhodnější nástroje. Dobré vybavení máme většinou k dispozici – CNC obráběcí stroj a CAM software. Doplňme jen myšlenku a vhodný nástroj – ¾ hodiny můžeme zvládnout i za 5 minut. Rychleji, a přesto bezpečněji…
Jan Matějíček, Seco Tools CZ s. r. o.
Seco Tools CZ, s. r. o.
Olomoucká 178a
627 00 Brno
Tel.: +420 530 500 811
Fax: +420 530 500 810
seco.cz@secotools.com
www.secotools.com/cz
Mohlo by se Vám líbit
Síla evoluce: ICONICS se mění na Mitsubishi Electric Iconics Digital Solutions
- Digitalizace
-
19. dubna 2025
Společnost ICONICS oznamuje oficiální změnu názvu na Mitsubishi Electric Iconics Digital Solutions (MEIDS), což představuje významný krok v jejím vývoji. Společnost MEIDS, s podporou společnosti […]
Milan Rajtár je novým šéfem největšího českého výrobního závodu Innomotics v Mohelnici
- Práce
-
17. dubna 2025
Společnost Innomotics vyvíjí a vyrábí ucelené portfolio nízkonapěťových a vysokonapěťových motorů, generátorů, převodových motorů, měničů pro střední napětí a vřeten. V České republice má téměř 4000 […]
Společnost Sandvik Coromant představila břitové destičky CoroCut® 2 s geometrií -RF pro vysoce přesné a bezpečné tvarové obrábění
- Obrábění
-
17. dubna 2025
Kromě toho do své nabídky zařadila také nástrojovou třídu GC1205 umožňující dosažení vynikajících výsledků při upichování a zapichování v žárovzdorných slitinách (HRSA) ve vystárnutém stavu […]