29. října 2019 10:41
Automatizace výroby rámu automobilu je cestou k úspěchu společnosti MAGNA Presstec
Od roku 1979 si razí Mercedes třídy G cestu lesem i polem, bahnem, štěrkem i sněhem.
Z tohoto důvodu se klade velký důraz na pevný žebřinový rám. Jejich výrobcem je společnost MAGNA Presstec v rakouském Lebringu nacházejícím se v blízkosti města Graz. Od roku 2017 je zde na lince navržené a vybavené průmyslovými roboty KUKA plně automatizovaná výroba nového faceliftovaného modelu. Specialisté obou podniků při její úpravě řešili řadu výzev, například zvláštní geometrické uspořádání výrobní haly, nebo velikost a váhu jednotlivých dílů.
Robustní, s dlouhou životností a k tomu nezaměnitelný vzhled: vnější podoba mercedesu třídy G se od jeho uvedení na trh změnila jen v detailech. Po posledních úpravách je tato offroad ikona o 53 milimetrů delší a o 121 milimetrů širší a působí tak na silnici i v terénu ještě atraktivněji. A to přesto, že technice se věnovala větší pozornost než vzhledu. Žebřinový rám, který dává automobilu potřebnou stabilitu a bezpečnost, byl v průběhu modernizace rovněž přepracován. Současně s poslední G-třídou začala nová éra jeho výroby. Tam, kde se dříve svařovalo ve velké míře ručně, převzala tyto práce automatizovaná výrobní linka od firmy KUKA.
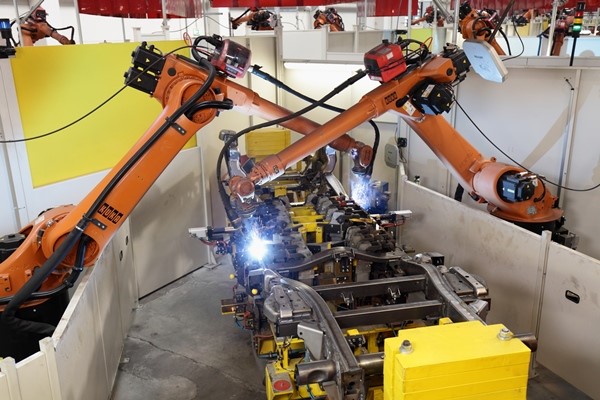
Foto 1 – Podélné a příčné nosníky se spojí a svaří, aby tak vytvořily přední, příp. zadní část
Zkušený partner pro automatizaci
„Pro nás to byl první případ spolupráce se společností KUKA,“ říká Armin Kleemaier, projektový manažer podniku MAGNA Presstec. Podnětem byla reference o systému realizovaném před několika lety firmou KUKA, který řešil podobné úkoly. Startovacím bodem společného projektu byl workshop. „Velice pozitivně na nás působila možnost vizualizovat cíle a nároky obou stran a poté jít spolu do jejich naplnění,“ vysvětluje Armin Kleemaier. Počáteční, v hrubých rysech načrtnutý koncept, určující, jak by mělo zařízení vypadat, se v průběhu prací na projektu postupně zpřesňoval a konkretizoval.
Opravdovou výzvou byla plocha výrobní haly. „Celková rozloha pro výrobu a logistiku činí přibližně 2000 čtverečních metrů, avšak ne veškerou podlahovou plochu lze využít pro výrobu. Kromě toho je výrobní hala velmi dlouhá a úzká,“ zdůrazňuje Dominik Pfeiffer, projektový manažer společnosti KUKA. Pro stísněné prostorové poměry bylo proto nutné najít individuální řešení. Například takové, že se musela na levé straně haly vytvořit zásobovací ulička pro kotouče s drátem nebo výbavu robotů. K odkládání jednotlivých dílů v průběhu výrobního procesu slouží regály.
K tomu se přidávají ještě problémy s rozměry a váhou jednotlivých dílů: při délce 4,30 metru a šířce 1,20 metru, váží žebřinový rám přes 230 kilogramů. Skládá se z přibližně 145 jednotlivých dílů a celková délka svarů činí přibližně 80 metrů. K tomu je zapotřebí připočíst ještě přes 200 bodových svarů.
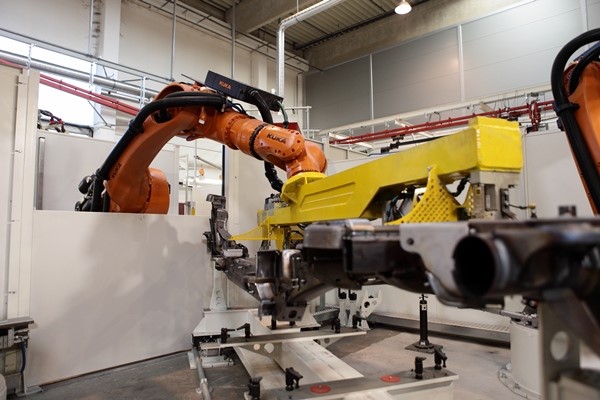
Foto 2 – Předávání na inline měřicí stanici k výstupní kontrole
Zařízení zhotovené na míru pro výrobu automobilového skeletu (body-in-white)
Žebřinový rám se skládá ze dvou hlavních dílů a dalších částí. Výrobní linky pro přední a zadní část jsou stejného systémového uspořádání, avšak zrcadlově souměrné. Důležitými částmi sestavy jsou dvě zařízení zvaná „Squeezing station“, která se na základě „Lessons learned“ z předchozích projektů a porad, konaných po celém světě, ukázala jako nezbytná. Obě části se spojují chytře promyšleným svařovacím postupem tak, aby vzniklo minimum deformací a napětí. V navazující, geometrii určující, tzv. „Geostanici“, se spojí podélné nosníky s příčnými a s pouzdry pro péra. Od tohoto okamžiku se hovoří o přední, příp. zadní části sestavy. Zvláštností je, že bodování a finální svařování se neprovádí v samostatných stanicích, ale vždy v příslušných sekcích výrobní linky. Po přivaření menších dílů se na konci linky podrobí celá sestava kontrole kvality, kterou provádí určený pracovník. Teprve poté umístí robot díl do regálu, odkud bude dodán k dalšímu zpracování.
V následující fázi se na přední a zadní konec připevní další díly, čímž vznikne šasi, resp. žebřinový rám. Poté se provede finální navaření připevněných dílů. Po výstupní kontrole, kterou provádí linkový měřicí systém a kontrolor, se předávají hotové žebřinové rámy k povrchové úpravě.
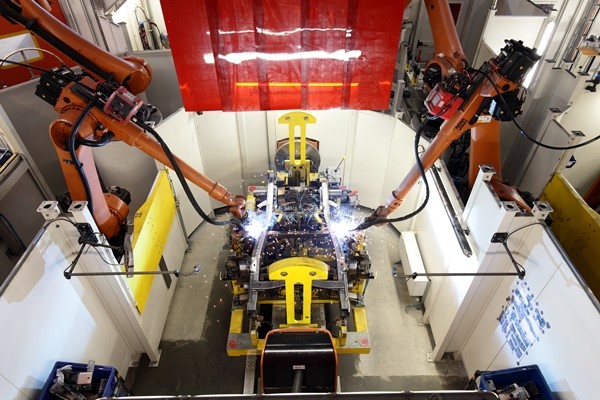
Foto 3 – Svařování drobných dílů pro přední a zadní část. Finální svařování se provádí přímo na lince, takže oddělené svařovací stanice nejsou zapotřebí.
Přesné řízení se systémem KUKA
Pro celý proces výroby byl použit řídicí systém Standard miKUKA. S vybavením miControl a miView, coby integrálními součástmi softwarového řešení, získávají koncoví zákazníci osvědčené a vyzkoušené stavební kameny řídicích programů. Ty umožňují uživatelům velmi rychle a bez větších nároků vytvořit a případně rozšířit funkce pro obsluhu a zobrazování. „S využitím tohoto řídicího systému jsou naši zákazníci schopni vyrábět podle standardů průmyslu 4.0. My zajišťujeme s naší řídicí technikou nezbytné propojení do sítí, autokonfiguraci a autodiagnózu,“ vysvětluje Dominik Pfeiffer.
Tisíce žebřinových rámů za rok
Od května 2017 je zařízení v provozu. „Svařovací procesy jsou stabilní a my dosahujeme s minimálním personálním osazením optimální kvality a rovněž i vysokého objemu výroby,“ shrnuje Dominik Pfeiffer. Je zde nasazeno 45 robotů, převážně typů KR 30 L16 pro svařování a KR240 pro manipulaci. Na koncové inline měřicí stanici kontroluje díly robot s kamerou a liniovým laserem a zabezpečuje 100% kontrolu všech rámů, pokud jde o jejich rozměry, jako jsou díry, svorníky, hrany a plochy. Tím je zajištěna konstantní kvalita všech dílů.
Společnost MAGNA Presstec dosahuje ve dvousměnném provozu objemu výroby 20 000 žebřinových rámů za rok. S jejím průběhem a výsledky je Armin Kleemaier spokojen. „Spolupráce se společností KUKA probíhala od počátku dobře a během času se dále zdokonalovala. Pokud se vyskytly nějaké rušivé faktory, vždy jsme je mohli úspěšně vyřešit. Tímto způsobem jsme přivedli náš projekt k úspěchu,“ říká na závěr.
Informace o společnosti KUKA
KUKA je automatizační globální společnost s obratem kolem 3,5 miliardy EUR a zhruba 14 200 zaměstnanci. Jako jeden z předních světových dodavatelů inteligentních automatizačních řešení nabízí KUKA zákazníkům vše, co potřebují, z jediného zdroje: od komponentů a výrobní buňky až po plně automatizované systémy pro automobilový průmysl, elektroniku, spotřební zboží, kovoobrábění, logistiku/e-commerce, zdravotnictví a služby robotického průmyslu. Společnost má sídlo v Augsburgu.
Více informací na: www.kuka.com
Fota z archivu: KUKA CEE GmbH, odštěpný závod
Mohlo by se Vám líbit
Síla evoluce: ICONICS se mění na Mitsubishi Electric Iconics Digital Solutions
- Digitalizace
-
19. dubna 2025
Společnost ICONICS oznamuje oficiální změnu názvu na Mitsubishi Electric Iconics Digital Solutions (MEIDS), což představuje významný krok v jejím vývoji. Společnost MEIDS, s podporou společnosti […]
Milan Rajtár je novým šéfem největšího českého výrobního závodu Innomotics v Mohelnici
- Práce
-
17. dubna 2025
Společnost Innomotics vyvíjí a vyrábí ucelené portfolio nízkonapěťových a vysokonapěťových motorů, generátorů, převodových motorů, měničů pro střední napětí a vřeten. V České republice má téměř 4000 […]
Společnost Sandvik Coromant představila břitové destičky CoroCut® 2 s geometrií -RF pro vysoce přesné a bezpečné tvarové obrábění
- Obrábění
-
17. dubna 2025
Kromě toho do své nabídky zařadila také nástrojovou třídu GC1205 umožňující dosažení vynikajících výsledků při upichování a zapichování v žárovzdorných slitinách (HRSA) ve vystárnutém stavu […]