01. října 2019 08:25
Inovativní řešení společnosti HEIDENHAIN pro výrobu nástrojů a forem
TNC řídicí systémy – široká nabídka funkcí pro výrobu perfektních forem
Základním požadavkem na výrobu nástrojů a forem je vždy přesnost. Minimální odchylky tvaru, které jsou v podstatě neměřitelné a pouhým okem neviditelné jsou dnes dále rozšířeny o požadavky na vyšší produktivitu a co nejnižší výrobní náklady. Splnit obě podmínky najednou není jednoduchý úkol. Spojení vysoké přesnosti a efektivní výroby je výsledkem celé řady výkonných funkcí řídicích systémů TNC společnosti HEIDENHAIN. Jejich použitím získává koncový uživatel v pravém slova smyslu ze svého stroje to nejlepší a stanovené požadavky na přesnost obrobku jsou tak samozřejmostí.
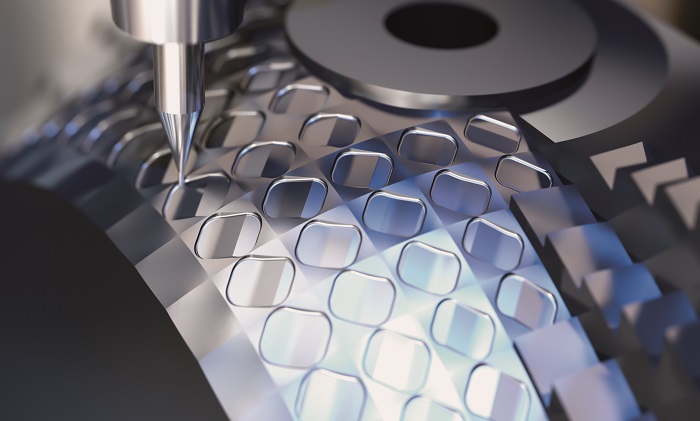
Cyklus 32 TOLERANCE a ADP (Advanced Dynamic Prediction) dvě funkce TNC, které zajistí optimální nastavení stroje a dráhy nástroje pro dosažení dokonalého výsledku při výrobě forem.
Optimální nastavení stroje před obráběním
Pomocí Cyklu 32 TOLERANCE může uživatel snadno nastravit stroj tak, aby se přizpůsobil odchylce dráhy T přesně podle tolerance výstupu z CAM software. TNC 640 předem rozpoznává změny směru a přizpůsobuje rychlost posuvu průběhu kontury a obráběnému povrchu. V Cyklu 32 TOLERANCE uživatel zadává do systému maximální povolené odchylky od ideální kontury. Použití tohoto cyklu nejen že zabraňuje poškození kontury ale zejména u takových kontur, kde často dochází ke změnám směru (typické pro volné nepravidelný povrch dílce) přímo ovlivňuje rychlost obrábění díky dosažení maximální rychlosti posuvu v dráze.
Někteří výrobci strojů nabízejí na základě cyklu 32 často také další podobné cykly. Například cyklus 332 dodatečně zohledňuje pro přizpůsobení odchylky dráhy T další specifická nastavení stroje od výrobce, např. pro hrubování, dokončování atd.
Další možnost jak optimalizovat obráběcí proces nabízí funkce ADP (Advanced Dynamic Prediction). Základem funkce ADP je především kvalita dat NC programu, funkce umožňuje optimalizované řízení pohybu posuvových os pro 2D až 5D frézování. Chyby v NC programu často vedou ke špatnému vedení dráhy a tím ke zřetelnému zhoršení kvality povrchu frézovaných obrobků. Pomocí ADP řídicí system TNC počítá kontury dynamicky dopředu a dokáže tak v ideální moment přizpůsobit rychlost pohybu os přechodům kontury díky takovému vedení dráhy, které omezuje zrychlení a trhnutí. Na základě toho lze hladký a perfektní povrch docílit v krátkých obráběcích časech, a to i při silně rozkolísaném rozložení bodů v sousedních drahách.
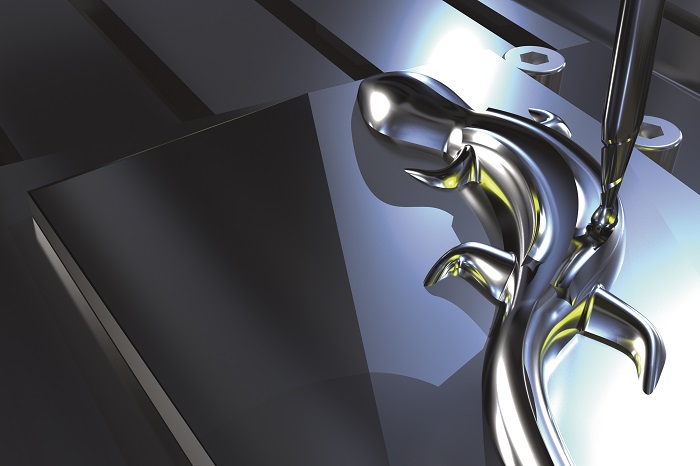
Funkční paket Dynamic Precision: Dokonalá souhra- kombinace dynamiky a vysoké přesnosti.
Optimalizace dynamické přesnosti frézovacího stroje
Funkční paket Dynamic Precision je zárukou vysoké dynamické přesnosti obrábění. Tato funkce minimalizuje síly působící na mechaniku stroje při obrábění a zároveň řeší odchylky na středu špičky nástroje (TCP). Balíček obsahuje celou řadu užitečných funkcí.
Součástí paketu je mimo jiné funkce CTC (Cross Talk Compensation), která řeší kompenzaci polohových odchylek TCP závislých na zrychlení. Zapnutí této funkce podporuje dynamickou stabilitu stroje a tím výrobu dílců s vysokou kvalitou povrchu a také zkrácení obráběcích časů.
Další užitečnou funkcí paketu Dynamic Precision je fukce pro aktivní tlumení dominantních nízkofrekvenčních vibrací – AVD (Active Vibration Damping). Tato funkce umožňuje rychlejší frézování bez nepříjemných vibrací a zároveň také minimalizuje obráběcí časy při trvalém zachování vysoké kvality povrchu. Kombinace uvedených funkcí CTC a AVD nabízí uživatelům ideální spojení požadavků na přesnost a rychlost obrábění. V praxi to pak znamená efektivní výrobu vysoce kvalitních složitých dílců.
Do paketu Dynamic Precision zařadíme také funkci LAC (Load Adaptive Control), která optimalizuje regulační parametry stroje v závisloti na zatížení a zajišťuje tak správnou dynamickou přesnost stroje. Výsledkem této funkce jsou také kratší obráběcí časy, protože posuvové osy dosahují požadovaných pozic rychleji. Mimo to funkce LAC kompenzuje změněné koeficienty tření a podporuje tak vysokou přesnost kontury.
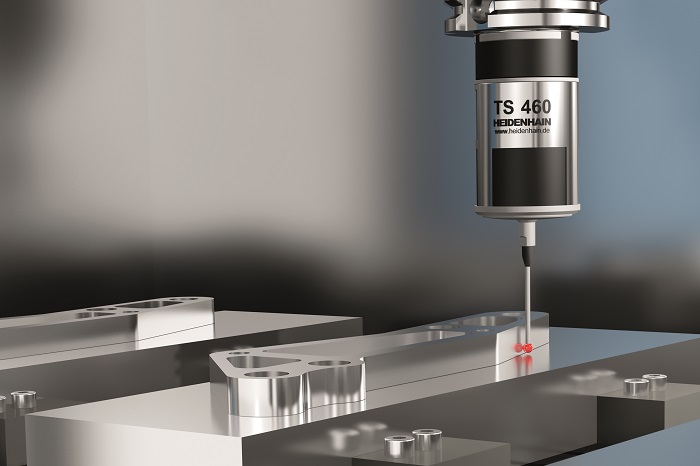
KinematicsOpt a 3D-ToolComp: přesnost stroje i nástroje je základním předpokladem pro výrobu vysoce přesných dílců
Jak efektivně implementovat požadavky na přesnost obrobku?
Požadavky kladené na přesnost zejména u pětiosého obrábění se neustále zvyšují. Komplexní dílce by tedy měly být vyráběny trvale s opakovatelnou přesností. Na výsledek obrábění působí celá řada faktorů, které přesnost zásadním způsobem ovlivňují. Například relativně silné kolísání teploty během obrábění má vliv na jednotlivé komponenty stroje a tím i výslednou přesnost. Tepelnou i mechanickou zátěž stroje lze poměrně snadno kompenzovat aktivací funkce KinematicsOpt. Při jejím zapnutí probíhá kontrolní měření středu kalibrační koule dotykovou sondou a zjistí se tak aktuální poloha středů rotace a následně je automaticky vykompenzována geometrie stroje. Na základně naměřených hodnot zjistí TNC systém prostorové chyby vyplývající z naklápění os. Cyklus vypočítá optimalizovaný kinematický popis stroje a uloží jej do paměti jako kinematiku stroje. Uživatel k tomu nepotřebuje prakticky žádné detailní znalosti, během několika minut je kinematika automaticky nastavena a uložena. Na výsledek obrábění má také ale samozřejmě vliv i geometrie nástroje. Díky funkci 3D-ToolComp a cyklu 444 podporuje řídicí system TNC výkonou korekci poloměru nástroje v závislosti na úhlu záběru. Odchylky úhlů se definují jako korekční hodnoty v tabulce automaticky po změření tvaru nástroje. TNC kompenzuje hodnotu poloměru, který je definován v aktuálním styčném bodu nástroje s obrobkem. K přesnému nastavení styčného bodu musí být NC program vytvořen CAM systémem s doplněnými normálovými vektory (LN příkazy). V LN příkazech je definován střed poloměru frézy a popřípadě take orientace nástroje vzhledem k povrchu obrobku. Důležitou pomůckou pro ověření přesnosti povrchu formy po obrábění je cyklus 444, který v automatickém režimu umožňuje proměřit polohu libovolných bodů nepravidelného povrchu dílce.
Sledování a plánování výroby
Pokud stroj zajišťuje bezproblémovou a optimální výrobu, jsou stejně optimální i navazující následné činnosti. Batch Process Manager je další výkonou funkcí řídicího systému TNC, s jejíž pomocí si jednoduše uživatel zorganizuje a naplánuje další průběh výroby přímo na řídicím systému. Díky této funkci uživatel naplánuje všechny zakázky velmi snadno a přehledně. Lze například zadat práce plánované na noční směnu, na celý den anebo i na blížící se víkend. Pokud řídicí systém zjistí problém (např. opotřebení nástroje), zobrazí Batch Process Manager předpokládaný okamžik ručního zásahu. Jednoduše tato funkce přebírá kontrolní funkci nad zásobou zakázek, které předem prověří. Uživatel si je tak jist, že mu nechybí nástroje, jaká je jejich životnost, získá informace o posloupnosti obrábění, jak bude stroj vytížen anebo kdy bude nutný ruční zásah. Své místo má především v bezobslužných směnách a při bezproblémovém zpracování čekajících zakázek v plně automatizovaném provozu.
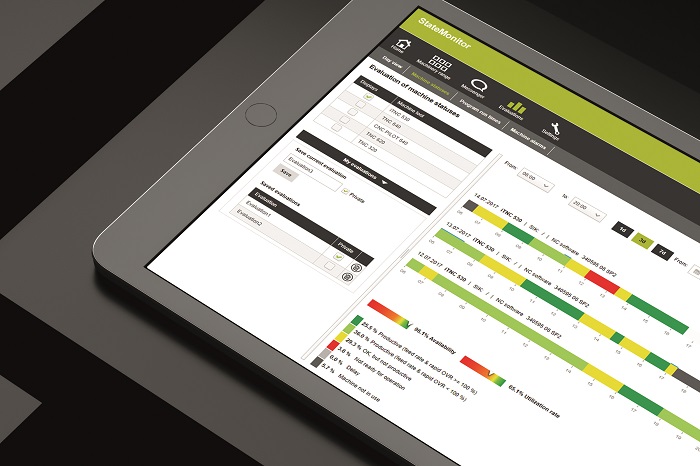
Batch Process Manager a StateMonitor společnosti HEIDENHAIN – podporují automatizaci a následné sledování výrobních procesů.
PC software StateMonitor umožňuje v reálném čase okamžitý přehled o aktuálně sledovaných a připojených strojích včetně monitoringu stavu zakázek. Software umožňuje zadávání údajů o strojích a dále poskytuje pomocí textových zpráv informace o stavu připojených strojů. Software může být nainstalován na všech zařízeních s webovým prohlížem. Uživatel ho pohodlně může využívat na počítači, chytrých telefonech nebo tabletech, ale samozřejmě i na řídicích systémech HEIDENHAIN ve formě rozšířené pracovní plochy tzv. Extended Workspace.
Mohlo by se Vám líbit
Síla evoluce: ICONICS se mění na Mitsubishi Electric Iconics Digital Solutions
- Digitalizace
-
19. dubna 2025
Společnost ICONICS oznamuje oficiální změnu názvu na Mitsubishi Electric Iconics Digital Solutions (MEIDS), což představuje významný krok v jejím vývoji. Společnost MEIDS, s podporou společnosti […]
Milan Rajtár je novým šéfem největšího českého výrobního závodu Innomotics v Mohelnici
- Práce
-
17. dubna 2025
Společnost Innomotics vyvíjí a vyrábí ucelené portfolio nízkonapěťových a vysokonapěťových motorů, generátorů, převodových motorů, měničů pro střední napětí a vřeten. V České republice má téměř 4000 […]
Společnost Sandvik Coromant představila břitové destičky CoroCut® 2 s geometrií -RF pro vysoce přesné a bezpečné tvarové obrábění
- Obrábění
-
17. dubna 2025
Kromě toho do své nabídky zařadila také nástrojovou třídu GC1205 umožňující dosažení vynikajících výsledků při upichování a zapichování v žárovzdorných slitinách (HRSA) ve vystárnutém stavu […]