11. září 2017 00:52
Zvýšená efektivita s hybridními nástroji
Obrábění podvozkových dílů – snazší, rychlejší a efektivnější
Obrábění podvozkových dílů není jednoduché, protože tento proces často zahrnuje materiály, jejichž opracování je velmi náročné. Podvozkové díly jsou také často dlouhé a štíhlé, což jejich obrábění ještě více ztěžuje. Společnost Walter AG se sídlem v Tübingenu je v této oblasti vyhledávaným partnerem. Společnost se s těmito specializovanými výzvami vypořádává díky efektivním geometriím a řadou důmyslných hybridních nástrojů, které nemají na trhu konkurenci.
Skříně ložisek pro přední kola auta jsou dlouhá 50 cm nebo více. Obvykle jsou vyrobeny z materiálů, jejichž obrábění je náročné. U osobních automobilů se obvykle používá hliník. Podvozkové díly užitkových vozidel se většinou vyrábějí z litiny a jejich rozměry jsou ještě větší. Kvůli délce a náročnému tvaru obrobku se skříně ložisek a další podvozkové díly velmi nesnadno obrábějí. Obzvláště proto, že obrobené díly – ať už se jedná o ložiska, ramena zavěšení, kyvná ramena, nebo pomocné rámy – budou muset zvládat mimořádně vysoké zatížení. Budou muset odolávat pohybům při řízení, stlačovat se a uvolňovat, zajišťovat bezpečné propojení s karoserií a perfektně pracovat i při těch nejnáročnějších jízdních podmínkách (a to je pouze několik z požadavků, které jsou na ně kladeny).
Robustní materiály
Materiály používané k výrobě podvozkových dílů jsou patřičně robustní, a tedy i špatně obrobitelné. Například ze slitiny hliníku, která v automobilovém průmyslu převažuje, mohou vznikat třísky často o délce 10 až 50 cm. Jejich hladký a čistý odvod je téměř nemožný.
Náročné je však již upnutí obrobku a prostorové požadavky na obrábění. Obrobek musí být pevně upnutý a přístupný, aby bylo možné obrábět všechny zamýšlené strany. Nástroj musí být dostatečně dlouhý, aby dokázal optimálně pracovat mezi svěrkou a dílem. Pro upínání a nástroje zde platí léty prověřené pravidlo: Tak dlouhé, jak je to nutné, ale tak krátké, jak je to možné. Nejdůležitější je ale držet pod kontrolou řezné síly. Délka obrobků i nástrojů může při obrábění způsobovat značný výkyv, který znemožňuje čisté a přesné zpracování.
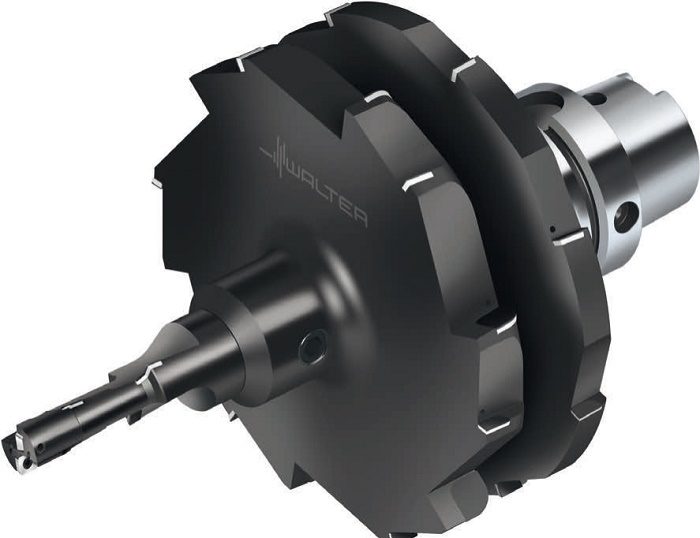
Kombinovaný nástroj na vrtání a frézování z PCD Simultánní čelní frézování horní a spodní strany horního spojovacího místo skříně ložiska. Do spoje se poté vyvrtá stupňovitý otvor bez výměny nástroje a ze zadní strany se interpolačním pohybem odstraní otřepy.
„Tomu ale lze úplně nebo částečně zabránit díky geometrii nástroje, speciálně vyvinuté pro tyto účely,“ vysvětluje Roland Hanischdörfer, produktový manažer pro speciální nástroje PCD společnosti Walter AG. „Naše nástroje jsou zkonstruovány speciálně pro obrábění podvozkových dílů.“
Existují v zásadě dva způsoby využití správné mikrogeometrie, které potlačují nežádoucí výkyv: stabilita nástroje může omezit výkyv na minimum či jej úplně eliminovat, nebo se síly vznikající při obrábění navzájem vyruší. Využití jednoho ze způsobů, nebo kombinace obou závisí na konkrétní situaci. „Naše nástroje zvládnou oboje,“ říká Roland Hanischdörfer.
Hybridní nástroje zvyšují efektivitu
To ale specialistům ve společnosti Walter nestačilo. Jejich zákazníci z automobilového průmyslu jsou přece vystaveni neustálému konkurenčnímu tlaku a jsou nuceni neustále hledat optimalizace. Společnost se sídlem v Tübingenu proto vyvinula širokou řadu nástrojů, které umožňují efektivní obrábění podvozkových dílů: hybridní nástroje kombinující vyměnitelné břitové destičky ze slinutého karbidu a břitové destičky z polykrystalického diamantu (PCD).
Karbidové vyměnitelné břitové destičky se používají k hrubování a dosažení mimořádně velkého obráběného objemu. Speciální geometrie nástroje také zajišťuje kratší třísky při obrábění hliníku a řeší tak problém s jejich odvodem.
V následujícím kroku obráběcího procesu je možné vyměnitelné břitové destičky PCD hybridního nástroje použít k dokončování. „Uživatel tak používá jeden jediný nástroj na dva naprosto odlišné kroky obrábění. Tím se zkracuje neproduktivní doba, protože není nutné nástroj vyměňovat.“
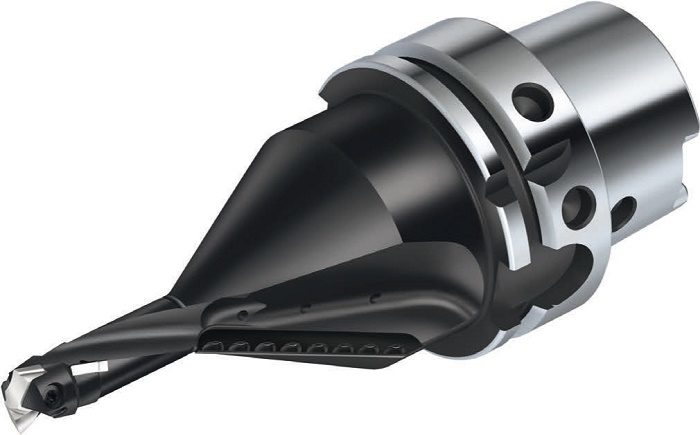
Kombinovaný nástroj z PCD Vrtání do plného materiálu s vyměnitelnou karbidovou vrtací destičkou pro šroubové napojení spojovací tyče. Dlouhá řezná hrana z PCD, navržená s geometrií na lámání třísek, se poté použije k vytvoření kuželové prohlubně a následně k odstranění otřepů z válcové části vyvrtaného otvoru interpolačním pohybem.
Podle Hanischdörfera zajišťují vyměnitelné břitové destičky PCD při dokončovacích operacích mimořádně vysokou jakost povrchu. Společnost Walter nedávno zařadila do své nabídky také nástroje PCD s lamačem třísek s diamantovou řeznou hranou. „Tím dosahujeme zkrácení metrových třísek na pouhých několik centimetrů.“ Mnoho hybridních nástrojů společnosti Walter je také uzpůsobeno k použití s minimálním mazáním (MQL). Namísto emulze nebo oleje, které se používají při konvenčním obrábění za mokra, zde ochlazuje a promazává obráběný povrch i nástroj směs olej–vzduch. To má několik výhod. Za prvé se díky použití MQL snižuje množství chladiva na hodinu z přibližně 500 l na pouhých 10 nebo 20 ml. A za druhé s MQL odpadá nutnost likvidace chladiva a mokrých třísek jako zvláštního odpadu, která je drahá a škodí životnímu prostředí.
Kompletní obráběcí koncepty
Odborníci ze společnosti Walter prokazatelně dosáhli u svých hybridních nástrojů při použití v praxi dlouhé životnosti a dobrých řezných parametrů. „Zákazníci, kteří tyto nástroje používají a vidí výsledky na svých obrobcích, řezných parametrech a životnosti nástrojů, jsou naprosto spokojeni,“ s potěšením říká Roland Hanischdörfer.
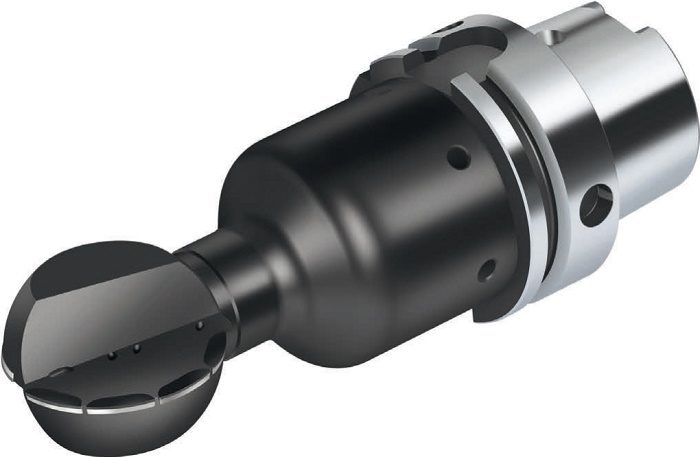
Pájená PCD kulová fréza Kulová fréza PCD pro vytvoření kulové pánve na ložisku kola, která zajistí volný pohyb ložiska kola
Zákazníci dokonce čím dál častěji po společnosti Walter požadují, aby na tomto základě vytvořila celé obráběcí koncepty. „Naši zákazníci potřebují řešení, která zlepší jejich efektivitu, ale nechtějí jejich vývoji věnovat příliš mnoho práce. Tento trend sledujeme již spoustu let. Proto své znalosti z oblasti obrábění kovů nyní využíváme nejen k vývoji vysoce efektivních nástrojů, ale také k tomu, abychom mohli našim zákazníkům nabízet kompletní obráběcí koncepty.“
K takovému konceptu obvykle vedou dvě cesty:
- Zákazník z automobilového průmyslu pozve odborníky Walter do své provozovny a ukáže jim digitální obrázky nebo prototypy nového dílu. Společnost Walter poté na základě toho vyvine kompletní obráběcí proces zahrnující veškeré nástroje.
- Uživatel přijde ke svému výrobci strojového vybavení a zakoupí si od něj kompletní obráběcí proces. Výrobce strojového vybavení se obrátí na společnost Walter s požadavkem na výběr a nákup nástrojů, které jsou k tomu potřeba. Nebo (viz výše) výrobce vyvine obráběcí koncept ve spolupráci s firmou Walter.
Ať už k cíli vede jakákoli cesta, základem je vždy co nejpodrobnější znalost stávajících obráběcích procesů a rámcových podmínek v provozovně zákazníka.
Čím dál více zákazníků vyžaduje od společnosti Walter ještě větší rozsah služeb: vývoj kompletních konceptů nákladů na díly. Klíčovým bodem je, že společnost z Tübingenu může zaručit konkrétní cenu na díl. To je zásadní výhoda obzvláště v automobilovém průmyslu, kde je „cena za díl“ (CPP) klíčovou proměnnou.
Vyžaduje to mimořádně úzkou spolupráci mezi společností Walter a příslušným uživatelem i rozsáhlou digitalizaci všech výrobních procesů a jejich zapojení do sítě. Roland Hanischdörfer vysvětluje: „Mají-li naši odborníci na digitální výrobu dostatečné množství dat, které jim umožní vytvářet podrobné transparentní procesy, mohou odkrýt doposud nepředstavitelný optimalizační potenciál a dosáhnout vynikajících zisků v otázce efektivity.“
foto: Walter AG
Walter na EMO 2017: pavilon 3, stánek B34
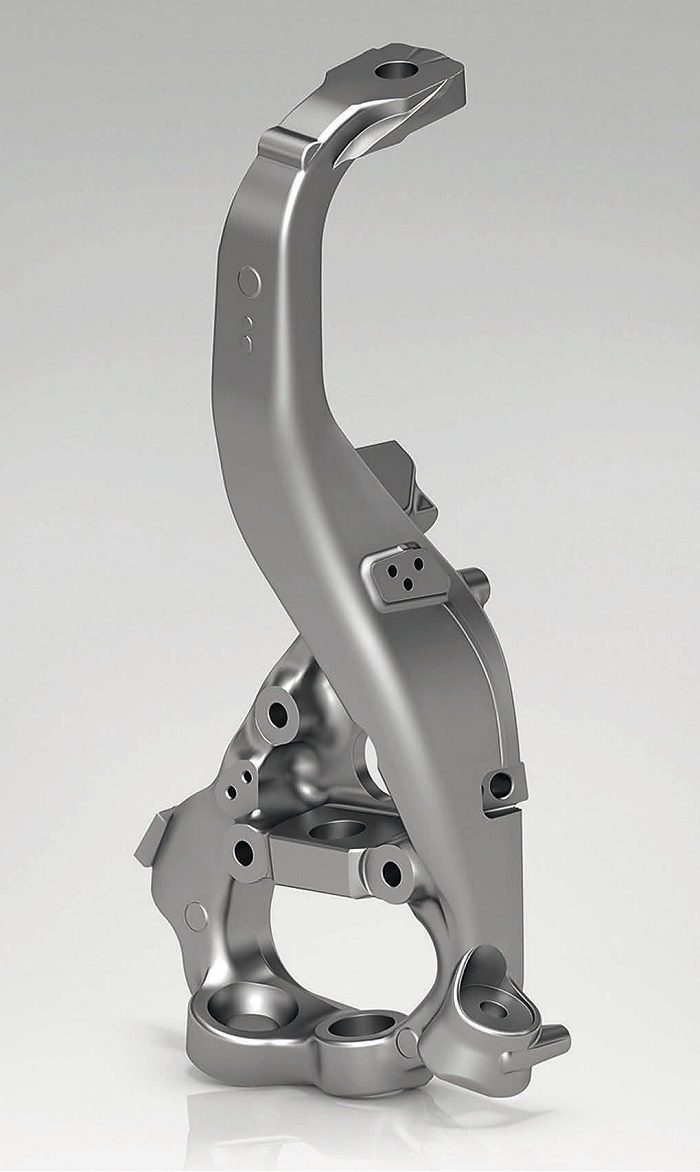
Hliníková skříň ložiska kola Ilustrační skříň ložiska kola z automobilového průmyslu, na kterou lze použít všechny výše uvedené nástroje
Mohlo by se Vám líbit
25 německých veletrhů v roce 2025
- Strojírenství
-
21. dubna 2025
Letošní veletržní sezona už začala v březnu, ale i tak jsou před námi desítky zajímavých oborově zaměřených průmyslových veletrhů. Inzerce Níže uvádíme přehled veletrhů, název, […]
Síla evoluce: ICONICS se mění na Mitsubishi Electric Iconics Digital Solutions
- Digitalizace
-
19. dubna 2025
Společnost ICONICS oznamuje oficiální změnu názvu na Mitsubishi Electric Iconics Digital Solutions (MEIDS), což představuje významný krok v jejím vývoji. Společnost MEIDS, s podporou společnosti […]
Milan Rajtár je novým šéfem největšího českého výrobního závodu Innomotics v Mohelnici
- Práce
-
17. dubna 2025
Společnost Innomotics vyvíjí a vyrábí ucelené portfolio nízkonapěťových a vysokonapěťových motorů, generátorů, převodových motorů, měničů pro střední napětí a vřeten. V České republice má téměř 4000 […]