26. září 2017 00:33
Nový vývoj v oblasti ergonomie technologie RTM
Úvod
V súčasnosti je väčšina priemyselných odvetví pod neustále zvyšujúcim sa tlakom a preto je nevyhnutné prispôsobovanie sa novým trendom vo výrobnom procese. Medzi technológie posledného obdobia bezpochyby patrí aj technológia Rapid Prototyping. Nespochybniteľné medzi najväčší prínos tejto technológie patrí rýchlosť výroby prototypu, podľa čoho nesie aj svoj názov, takmer nulový odpad a taktiež použite materiály, ktoré sú netoxické. Pre firmy, ktoré sa zaoberajú vývojom a testovaním nových produktov, je použitie tejto technológie takmer samozrejmosťou. Pred spustením hromadnej výroby, ktorá vyžaduje vysoké investície, je možné vyrobiť prototyp v krátkom časovom intervale a tak overiť jeho tvar, rozmery, funkč nosť a iné vlastnosti.
Charaktristika technológie FDM
Metóda Fused Deposition Modeling je zaraďovaná k moderným a progresívnym technológiám k výrobe najmä prototypových dielov. Použiť ju je možné pre výrobu konkrétneho jedného dielu, ale aj pre vytvorenie nerozoberateľných spojov s možnosťou pohybu. Doba trvania tlače je závislá od veľkosti modelu a jeho tvarovej zložitosti, čo môže byť aj niekoľko hodín. Použitím tejto technológie je možné reálne ušetriť až 80 % celkových nákladov spojených s výrobou prototypu. Úspora je v tomto prípade tiež závislá na veľkosti modelu, ale aj na type pôvodnej konvenčnej výroby. Princíp činnosti je založený na postupnom natavovaní termoplastu. Ten je navinutý na cievke v podobe drôtu a do trysky je podávaný pomocou mechanizmu s ozubeným prevodom. Model je vytváraný postupným nanášaním v jednotlivých vrstvách cez trysku, kde bol stavebný materiál ohriaty na teplotu vyššiu ako je teplota tavenia. Roztavený materiál okamžite tuhne po styku s podložkou. Pri vytváraní zložitejších modelov môže byť potrebné využitie podporných konštrukcií, ktoré zabraňujú tomu, aby sa model počas výroby zrútil pod vlastnou váhou. Tieto podpery sú odstránene po dokončení a vybrané zo zariadenia, a to buď mechanicky, alebo chemicky za použitia vhodného rozpúšťadla. Hlavným pôsobiskom využitia takto vyrobených súčasti sú testy funkčnosti a dizajnu, ale pre svoje dobré mechanické vlastnosti je možné ich použiť ako finálne výrobky, ktoré sú schopné zvládať reálne zaťaženie. Hlavnou výhodou je vznik len veľmi malého množstva odpadu, ten vzniká pri nutnosti využitia podporných konštrukcii. Medzi nevýhody môžeme zaradiť zmršťovanie modelu počas chladnutia, a tým vznik tvarovej nepresnosti, to je ale možné odstrániť použitím korekcii v etape návrhu. Ďalšou nevýhodou pri použití metódy Fused Deposition Modeling je obmedzená presnosť, tento parameter je závislý od veľkosti použitých trysiek, cez ktoré je stavebný materiál vytláčaný.
Návrh a výroba komponentu pre tieniacu techniku
Vyrábaným komponentom bolo závažie pre vertikálne žalúzie. Tento komponent plní dve základné funkcie. Prvou jeho funkciou je, že slúži ako závažie pre látkové vertikálne žalúzie. Svojím umiestnením v spodnej časti tak napína látku a drží ju v správnom tvare. Druhou funkciou je úloha spájacieho prvku, kde pomocou úchytov, ktoré sú umiestnené oproti sebe, a spájacích lán je celá sústava spojená. Vďaka kladkovému mechanizmu je potom možné týmito žalúziami pohybovať v horizontálnom smere podľa potreby. Problémom pri tomto komponente je nedostatočná mechanická pevnosť pri nárazoch v mieste úchytu a následné poškodenie spájacieho prvku, čo má za následok nefunkčnosť celého mechanizmu, ktorý zabezpečuje horizontálny pohyb. Na obrázku 1 je pôvodný model závažia.
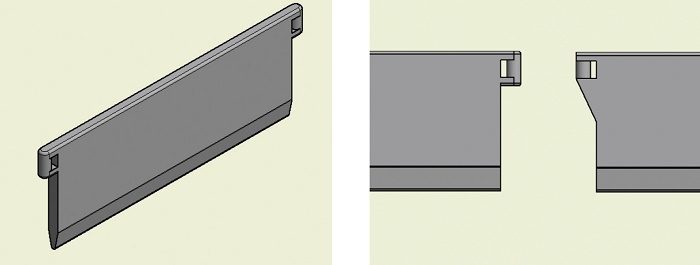
Obrázok 1: Pôvodný model závažia
Obrázok 2: Porovnanie pôvodného modelu a navrhovanej alternatívy
Základom pre výrobu súčiastky je model, ktorý bol vytvorený v programe Autodesk Inventor. Pri návrhu tohto modelu boli brané do úvahy požiadavky na základné funkcie budúcej súčiastky. Medzi základné požiadavky patrí celková veľkosť súčiastky, veľkosť úchytu pre spájací mechanizmus a osová vzdialenosť medzi týmito protiľahlými úchytmi. Pri výrobe technológiou FDM sú možnosti tvarovej zložitosti takmer neobmedzené, ale čím zložitejší tvar, tým sa výroba stáva zdĺhavejšia a s tým rastie aj cena výroby. Ďalšou požiadavkou z hľadiska pevnosti je, aby súčiastka bola vyrobená v celku a nie po častiach, a následne zmontovaná. V navrhovanej alternatíve je rozdiel oproti pôvodnému modelu v zmene spodnej časti úchytu, ktorá bola vymenená za rebro. Tento zásah nemá vplyv na funkčnosť a použiteľnosť komponentu, mal by však priniesť zvýšenie odolnosti proti mechanickému namáhaniu a tak zabezpečiť dlhšiu životnosť. Rozdiel je znázornený na obrázku 2.
Výber materiálu
Výber správneho materiálu závisí od budúceho použitia súčiastky a je to dôležitý parameter výrobného procesu. Pre navrhovanú súčiastku, ktorá slúži ako závažie v tieniacej technike, sú hlavnou požiadavkou mechanické vlastnosti, a to najmä odolnosť proti nárazu. Prostredie, v ktorom je táto súčasť využívaná, si nevyžaduje žiadne špeciálne vlastnosti ako vysoká tepelná odolnosť alebo biokompatibilita. Pre výrobu prototypu bol vybraný prírodný polymér PLA. Tento materiál má oproti termoplastu ABS lepšiu priľnavosť, vďaka čomu je možne tlačiť modely s vyššou presnosťou. Medzi ďalšie dôvody pre výber tohto materiálu patrí relatívne nízka cena a veľmi dobrá dostupnosť. Súčiastka vyrobená z tohto materiálu sa dá ďalej opracovávať konvenčným spôsobom. Pre potreby 3D tlače je tento materiál dodávaný najčastejšie v podobe struny s priemerom 1,75–3mm.
Simulácia mechanického zaťaženia
Pri posudzovaní konštrukčných úprav a ich vplyvu na mechanické vlastnosti bola využitá pevnostná analýza pomocou simulácie v programe Autodesk Inventor. Účelom tejto analýzy je overenie správnosti konštrukčného návrhu, prípadné odhalenie hrubých chýb a overenie životaschopnosti daného návrhu. Obidva modely boli zaťažené rovnakými silami. Pri simulácii bol nastavený materiál PLA. Pre porovnanie modelov bola zvolená zaťažujúca sila 500 N, ktorej miesto pôsobenia bolo zvolene v mieste úchytu. Ďalšie parametre, ktoré je potrebné nastaviť, sú veľkosť mriežky a väzby. Simulácia bola pri oboch modeloch spustená s rovnakými nastaveniami.
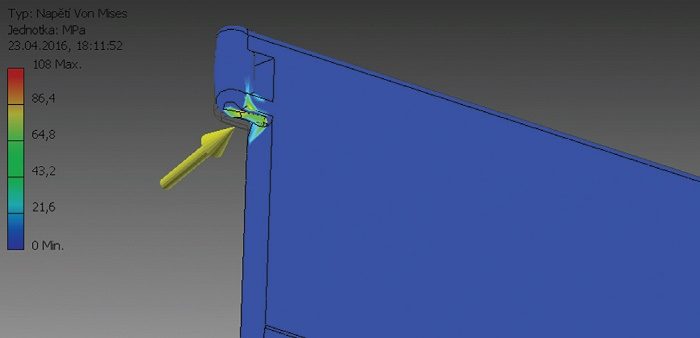
Obrázok 3: Priebeh napätia Von Mises pôvodného modelu
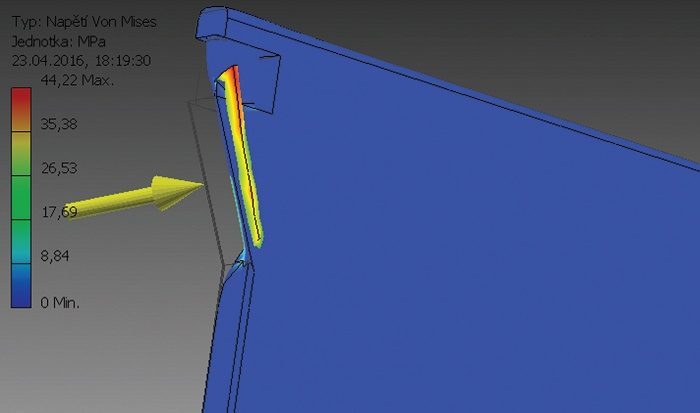
Obrázok 4: Priebeh napätia Von Mises navrhnutého modelu
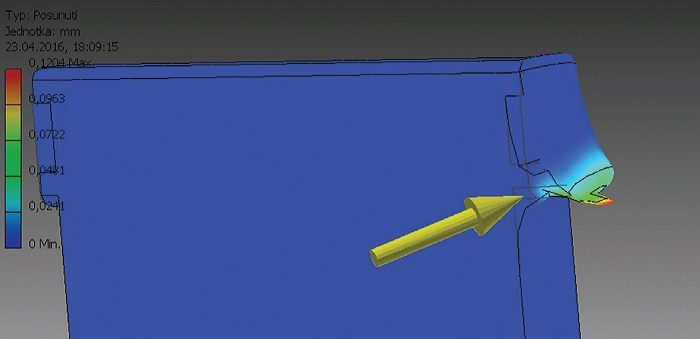
Obrázok 5: Celkové posunutie pôvodného modelu
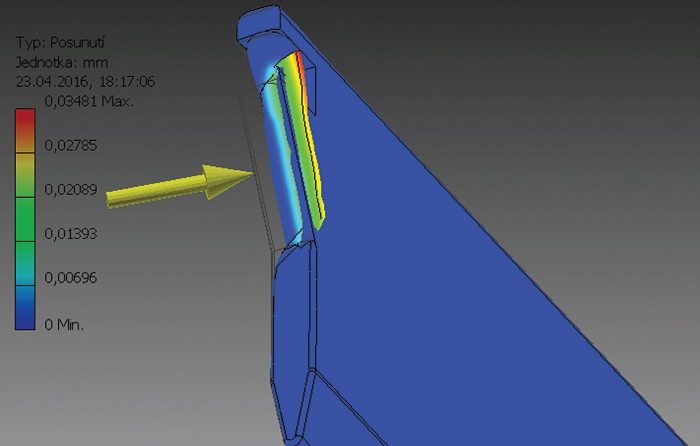
Obrázok 6: Celkové posunutie navrhnutého modelu
Porovnávanými parametrami v pevnostnej analýze boli maximálne napätie pôsobiace v zaťaženom mieste a celkové posunutie. Zrealizovaná konštrukčná úprava priniesla požadovaný efekt v podobe zníženia maximálneho napätia a celkového posunutia. Na obrázku 3 a 4 sú znázornené priebehy napätí pôsobiacich v kritickom mieste. Maximálna hodnota napätia klesla z pôvodných 108 MPa na 44,22 Mpa. Porovnanie celkového posunutia je zobrazené na obrázkoch 5 a 6, kde sa maximálna hodnota posunutia znížila z 0,1204 mm na 0,03481 mm.
Výroba komponentu
Preprocesing – Do tejto etapy výroby patria operácie predchádzajúce samotnú tlač. Navrhnutý model bol pomocou CAD programu Autodesk Inventor konvertovaný do potrebného formátu „.stl“. Samotný prevod ponúka z dvoch možných variant výstupu: „Binárny“ a „ASCII“. Zvolený bol binárny formát. Ďalší krok je nastavenie rozlíšenia, kde bola vybraná možnosť „Stredné“. Takto je model prevedený do požadovaného formátu. Pomocou programu MiniMagics bola následné skontrolovaná polygónová sieť modelu. Pre nastavenie parametrov tlače a tlač bol využitý program Sli3cr. Tento program patrí do kategórie „open source“ a je voľne šíriteľný. Kde v prvom kroku bol importovaný vytvorený model vo formáte „.stl“. Program Sli3cr vypočíta dobu potrebnú na vytlačenie modelu spolu s ďalším údajmi o tlači, ako je počet potrebných vrstiev a podobne. Etapa preprocesing sa týmto končí a virtuálny 3D model je pripravený na výrobu. Pri výrobe bola použitá RepRap 3D tlačiareň. V etape výroby prebieha samotná tlač 3D modelu z virtuálnych dát. Celý priebeh výroby je možné sledovať v programe Sli3cr, kde je znázornená animácia priebehu s údajmi, ako napríklad, kde sa nachádza tlačová hlava, zostávajúci čas výroby, potrebné množstvo materiálu, teplata trysky atd.
ZÁVER
Cieľom predkladaného príspevku bolo analyzovanie vplyvu konštrukčných zmien na vybranom komponente, ktorého využitie je v tieniacej technike. Pre potreby 3D modelovania a simulácii mechanického zaťaženia bol použitý 3D program Autodesk Inventor a jeho nadstavby. Pôvodný model aj navrhovaná alternatíva boli v kritickom mieste zaťažené porovnávacou silou 500 N. Z výsledkov napäťovej analýzy vychádza, že navrhovaný model bude odolnejší voči mechanickému zaťaženiu. Ako výstupy pre porovnanie výsledkov napäťovej analýzy boli brané do úvahy parametre: celkové posunutie a napätie Von Mises. Navrhovaný model bol reálne vyrobený pomocou technológie Fused Deposition Modeling, ktorá patrí do súboru technológii Rapid Prototyping.
Ing. Tomáš Coranič, doc. Ing. Štefan Gašpar, PhD., prof. Ing. Ján Paško, Csc.
Použitá literatúra
1. MARCINČIN, J. N. – KURIC, I. – LEGUTKO, S. – MARCINČINOVÁ, Ľ. N.: Computer Aided Technical Preparation of Production. Poznan University of Technology, Poznan, 2011, 262 p., ISBN 978-80-89276-29-5.
2. NOVÁKOVÁ-MARCINČÍNOVÁ, Ľudmila – NOVÁK-MARCINČIN, Jozef: Zlepšovanie mechanických vlastností súčiastok vyrábaných technológiou Rapid Prototyping – 1. vyd. – Košice: TU – 2013. – 76 s. – ISBN 978-80-553-1519-5
3. MARCINČIN, J. N. – BARNA, J. – MARCINČINOVÁ, Ľ. N. – FEČOVÁ, V.: Analyses and Solutions on Technical and Economical Aspects of Rapid Prototyping Technology. Tehnički vjesnik – Technical Gazette, Vol. 18, No. 4, 2011, pp. 657–661, ISSN 1330-3651
4. PACURAR, R. – BALC, N. – BERCE, P.: Research on improving the mechanical properties of the SLS metal parts. In: Annals of DAAAM for 2008 & Proceedings of the 19th International DAAAM Symposium, Book Series: Annals of DAAAM and Proceedings, 2008, p. 1003-1004
5. SEDLÁK, J., PÍŠA, Z. Rapid Prototyping master modelů pomocí CAD/CAM systémů. In Mezinárodní vědecká konference 2005. Ostrava: VŠB TU Ostrava, Fakulta strojní, 07. 09. 2005–09. 09. 2005. [vid 2013-04-10], 30s.,ISBN: 80-248-0895-1.
6. PÍŠKA, Miroslav. Speciální technologie obrábění. Vyd. 1. Brno: Akademické nakladatelství CERM, 2009, 247 s. ISBN 978-80-214-4025-8.
Mohlo by se Vám líbit
Nová vlajková loď generátorů libovolných průběhů s šířkou pásma 3,9 GHz a výstupní rychlostí 10 GS/s
- Elektro
-
12. července 2025
Společnost Spectrum Instrumentation představuje čtyři nové vysoce výkonné generátory libovolných průběhů (AWG), které jsou významným milníkem v nabídce jejích produktů. Nové generátory AWG jsou určené […]
Cílem je stát se jedničkou pro oblast kabelů
- Elektro
-
10. července 2025
Společnost KONEKA, která vznikla vloni na podzim jako dceřiná společnost PRAKAB (PRAKAB Pražská Kabelovna s.r.o.), plánuje v letošním roce dále rozšiřovat své služby a produktové portfolio. […]
Každý den je jinak BAREVNÝ!
- Plasty
-
08. července 2025
Chcete si pověsit na zeď něco barevného a užitečného? Připravili jsme pro Vás nový plakát se základními informacemi o barevném prostoru CIELab a výpočty ΔE […]